Protecting Our Most Valuable Tools: Hand Safety in the Mining Industry
June 14, 2022 - The rugged conditions of mining sites bring a unique set of safety concerns, from chemical and mechanical hazards, to heavy loads and vibrational impact. Workers use their hands on a daily basis for tasks such as welding, cutting, and operating complex machinery, and so gloves are an important piece of protective equipment on every mine site. In this article, Blackwoods’ National Category Manager for Safety, Shane Wood, discusses the importance of prioritising hand safety, and ways that glove design is adapting to meet every day on-site challenges.
Wrist and hand injuries account for a large portion of work-related hospitalisation across industrial sectors. Depending on the severity of the injury, hands are difficult to mend due to their complex bone, tendon and ligament structure. This can affect the individual’s ability to continue with the same type of work following recovery. With such risks on the table, it is imperative that mining sites prioritise fit for purpose hand protection for the application and task.
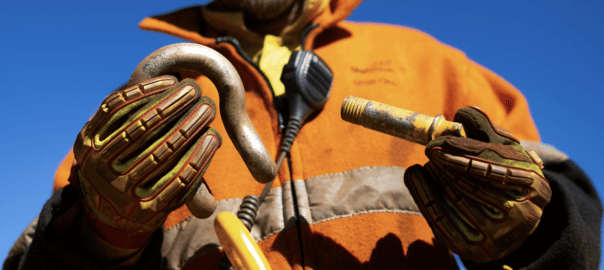
“PPE and gloves are a last line of defence for one of our most valuable tools in mining work – our hands,” explains product expert, Shane Wood. “Despite this, hand safety is frequently overlooked when we’re in a rush, which is why Australia has such high rates of hand injuries, especially amongst industrial employees.”
While larger companies in the mining space have some of the highest protocols around employee Health and Safety, smaller to mid-level operations rely on PPE distributors and glove manufacturers to advise on product suitability. This is based on the standards markings on the glove, which are sometimes unclear. According to Shane, it can be hard to identify which gloves are best suited to the application by only using these markings.
“Standards approvals and glove markings can get quite confusing,” he explains. “In Australia, for performance testing on mechanical hazards such as abrasion, two different cut tests, tear, puncture and impact, we rely on AS/NZS 2161.3, which is a direct adoption of the European standards EN388:2016. Some glove brands in the Australian market will be marked with these AS/NZS ratings, while all global brands sold in Australia will only have the European EN388 markings on the gloves.”
“They are both tested the same way, but it causes a bit of a grey area and instances of confusion for the user,” Shane continues. “If any glove is tested by a third-party certified laboratory, then either marking of AS/NZS or EN should give users peace of mind that the gloves performances levels have not been overstated.”
In addition to cuts and abrasions, high vibration or repeated blunt impact to hands can develop flow-on effects and pain throughout other areas of the body including shoulders, backs, and the abdomen. Manual handling also comes with common risks like pinched fingers – something that is often considered just “part of the job,” but that can be mitigated by impact resistant gloves.
“The most important thing is making sure that gloves are fit for purpose,” says Shane. “Matching the right equipment to the right application means that you are getting the best possible protection. If you are wearing gloves that are too bulky when working with small parts, chances are you’ll just end up taking them off out of frustration.”
“The tricky part is ensuring full protection without hindering mobility,” he continues. “Depending on the work that is being done, the gloves might need stronger grip, chemical resistance, impact or pinching protection et cetera. There is no one glove to rule them all – it is about catering to the specific task and weighing up safety with efficiency.”
Balancing affordability expectations, compliance, and user comfort is the biggest challenge for PPE manufacturers as they contend with minimising restricted dexterity for handling tasks. Shane posits that as fibre and production technologies advance, gloves are becoming even more tailored to market needs.
“Advancements in manufacturing techniques and materials are getting better all the time. We have unique factors to consider in Australia as well; wearing gloves in warmer areas like Western Australia or Northern Queensland is going to be uncomfortable, so breathability is key. Seamless knits and abrasion-resistant fibres like high-density polyethylene (HDPE) can help with that.”
Supplying the industry with timely and flexible solutions also involves paying attention to changing practices like software integration.
“We are seeing such innovative approaches to glove design recently, especially as digitalisation becomes part of industrial operations. As automation became more common on mine sites, we noticed that gloves would come off to use interfaces or phone screens, and then people would forget to put them back on. So touch-screen compatible fingertips are definitely a hugely beneficial design element that is becoming more popular.”
Blackwoods strongly advocates for stringent field testing of all PPE, and relies on end-user feedback to offer the best products to the Australian mining sector. To learn more about hand protection and safety wear, Shane recommends reading the latest issue of the Safety Spotlight Magazine, available to order or read online.