Maximizing Uptime in Aggregate and Mining Operations: The Role of Urethane Wear Parts
June 15, 2025 - In the aggregate and mining industries, downtime is the enemy of productivity. Frequent equipment wear and tear can lead to costly maintenance, unplanned shutdowns, and reduced operational efficiency. Choosing the right wear parts is critical to keeping production lines running smoothly. Urethane wear components have emerged as a superior solution for extending equipment lifespan and minimizing downtime.
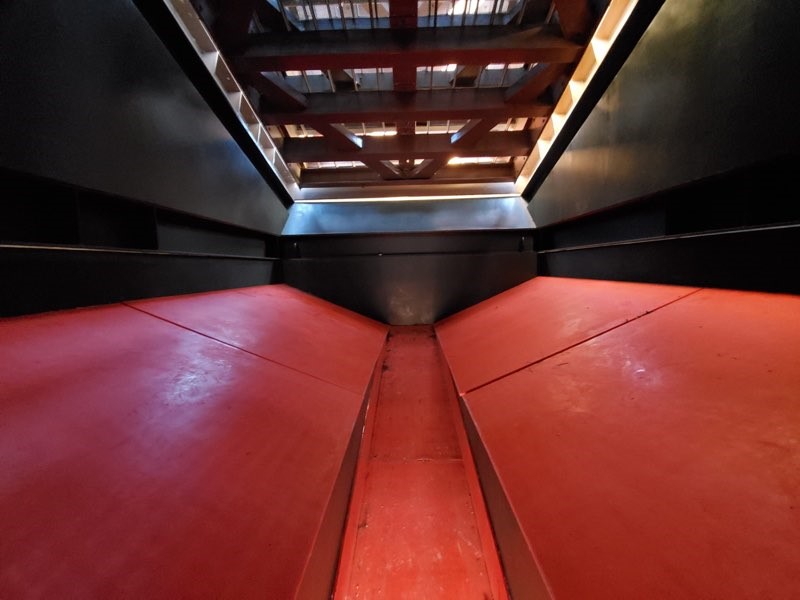
Common Wear Challenges in Aggregate and Mining
Mining and aggregate processing involve extreme operating conditions, including:
-High-impact forces from heavy loads
-Continuous exposure to abrasive materials
-Harsh environmental conditions, including moisture and temperature fluctuations
-Frequent maintenance and replacement of wear parts due to premature failure
Why Urethane? A Game-Changer for Wear Protection
Urethane wear parts offer a unique combination of durability, flexibility, and resistance to wear, making them an ideal choice for mining and aggregate applications. Key advantages include:
-Superior Abrasion Resistance
Urethane parts outperform rubber and steel in high-wear environments, significantly reducing material loss and increasing lifespan.
-Impact Absorption & Flexibility
Unlike steel, which may crack under heavy impact, urethane absorbs shocks and resists deformation, making it ideal for screening and impact zones.
-Corrosion and Chemical Resistance
Urethane resists exposure to moisture, chemicals, and harsh environments, reducing the risk of premature failure compared to metal wear parts.
-Noise Reduction
Urethane components help reduce operational noise, creating a safer and more comfortable work environment.
-Lightweight & Easy Installation
Lighter than steel, urethane parts are easier to handle and install, reducing labor costs and improving maintenance efficiency.
-Real-World Benefits: Durex Urethane Solutions in Action
Many aggregate and mining operations have successfully transitioned to urethane wear parts, resulting in longer equipment lifespans and improved efficiency. Some key applications include:
Screening Media – Durex’s modular urethane screen panels provide enhanced wear life while maintaining high material throughput.
Wear Liners & Impact Pads – Reduce impact damage and prevent material buildup in transfer points and chutes.
Best Practices: Maximizing Urethane Wear Part Performance
To get the most out of urethane wear components, consider these tips:
-Choose the right formulation based on the specific application needs (abrasion, impact, or chemical resistance).
-Perform regular inspections to monitor wear and replace parts before they reach critical failure points.
-Follow proper installation techniques to ensure secure fitting and optimal performance.Consult with Durex experts to determine the best wear solutions tailored to your operation.
Conclusion: A Smarter Investment in Productivity
By switching to urethane wear parts, aggregate and mining operators can significantly reduce downtime, cut maintenance costs, and improve overall efficiency. Durex Products offers a full range of high-performance urethane solutions designed to withstand the most demanding conditions.
Looking to maximize uptime and extend the life of your equipment? Contact Durex Products today to find the right urethane wear solutions for your operation: Phone: 715-483-9611.
Email: customerservice@durexproducts.com